
IN-HOUSE
MANUFACTURING
OUR MANUFACTURING PROCESS
At D.Navin, we take immense pride in our in-house diamond manufacturing process, which transforms responsibly sourced rough diamonds from industry leaders such as, Rio Tinto and De Beers Group into beautiful diamonds. Our craftsmanship ensures each diamond's brilliance, clarity, and quality. Here's an overview of our step-by-step process:
STEP 1
SOURCING
We begin by responsibly sourcing our rough diamonds from trusted mining companies such as Rio Tinto and De Beers Group. Our commitment to ethical and sustainable practices ensures that our diamonds have a transparent and responsible supply chain.
STEP 3
SORTING
Our experts categorize the rough diamonds based on size, shape, and quality to strategize the best polishing approach.
STEP 5
CLEAVING & SAWING
Using precision tools, we execute the cutting process, either by cleaving (splitting) or sawing, to create smaller pieces known as "roughs."
STEP 7
FACETING
Our skilled artisans develop a comprehensive facet plan, and then use employ state-of-the-art cutting machines to meticulously cut and polish each facet, including the table, crown, girdle, and pavilion facets.
STEP 9
INSPECTION
We subject the polished diamond to thorough scrutiny under magnification and specialized lighting to identify any imperfections or flaws.
STEP 11
PACKAGING
Each polished diamond is thoughtfully and securely packaged, ready for shipping, external certifications or presentation to our valued customers.
STEP 2
INSPECTION
After sourcing, we carefully examine the rough diamonds, evaluating their potential while identifying any flaws, inclusions, or unique characteristics.
STEP 4
MARKING
We mark each rough diamond to determine the optimal orientation for cutting, aiming to maximize yield and brilliance.
STEP 6
BRUTING
We refine the rough diamond's shape by meticulously grinding away excess material from the edges. Then we use our bruting machines to shape the diamond into its fundamental form.
STEP 8
POLISHING
Using a carefully selected abrasive, we gently grind and polish each facet of the diamond, enhancing its brilliance and clarity.
STEP 10
GRADING
Our experts assign a precise grade to each diamond, adhering to the "Four Cs" (carat weight, cut, color, and clarity).
STEP 12
DISTRIBUTON
Our diamonds are carefully distributed to all of our sales offices around the world some of which include; Mumbai, New York, Dubai, Antwerp, Hong Kong and Shanghai.

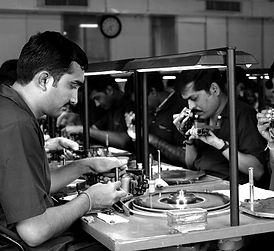_edited.jpg)



OUR COMMITMENT
Our commitment to excellence extends to our in-house manufacturing facilities in Surat, where the magic of transforming rough diamonds into exquisite polished gems takes place. Equipped with cutting-edge technology and adhering to the highest industry standards, our factory follows the Best Practice Principles (BPP) and Responsible Jewellery Council (RJC) compliance, ensuring ethical practices and sustainability throughout the production process.
With a team of over 4000 skilled artisans, each possessing a profound understanding of the artistry involved, we create masterpieces that radiate brilliance and perfection. Their expertise, coupled with our unwavering dedication to quality, results in polished diamonds that exemplify precision, beauty, and integrity.